Complex procedures are required to process mineral rock, rock dust, binder (bitumen) and additives into an asphalt mixture.
There are numerous safety aspects to observe and great challenges for man and machine in the production process. Fluctuating temperatures and dirt and dust need to be handled. Continuous lubrication of machine elements is a key factor in preventing machine breakdowns and ensuring high productivity for the whole system.
Challenges
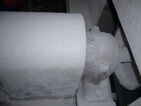
Dust, dirt, vibration
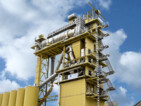
Different lubrication points require different lubricants and lubricant amounts
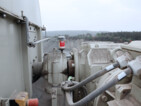
Varying temperatures
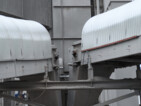
Hard-to-reach lubrication points
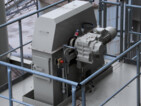
High energy costs
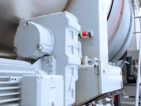
Rotating machine parts hazard
Solutions
Mount a perma lubrication system at the lubrication point. Depending on the conditions prevailing at the lubrication point, the perma lubrication system can either be mounted directly or remotely.
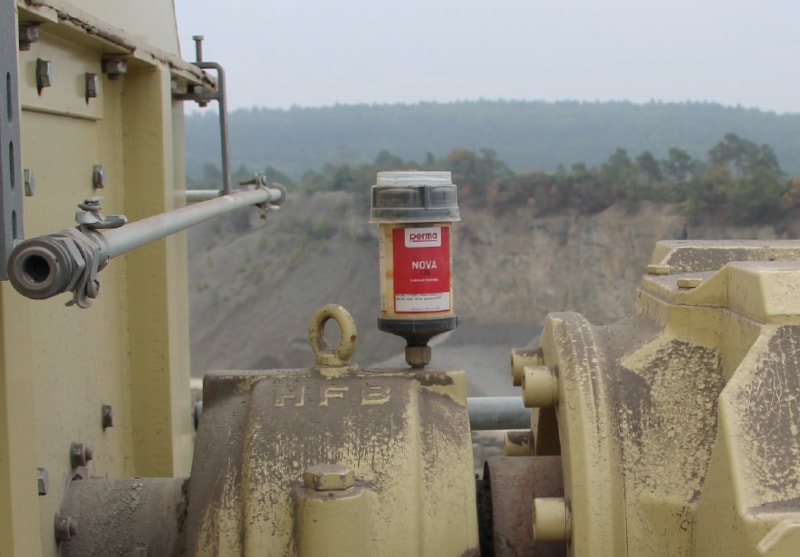
- Electronic control unit with temperature compensation
- System operates reliably from -20 °C to +60 °C
- Dust-tight and protected against water jets
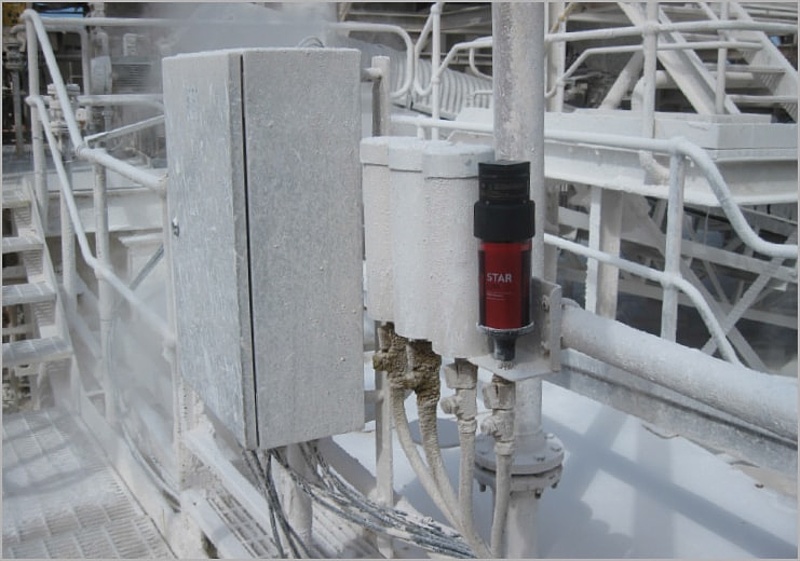
- For lubrication with strong vibration / shocks (isolation of lubrication system)
- When workers’ safety is at risk: Mounting in safe areas
- For hard-to-access lubrication points
Any more questions?
Simply contact us by phone or email for an individual consultation on asphalt mixing plants.
Advantages of automatic lubrication
Reduces wear
Continuous relubrication at short intervals reduces wear and seals lubrication points to prevent contamination from dust and dirt
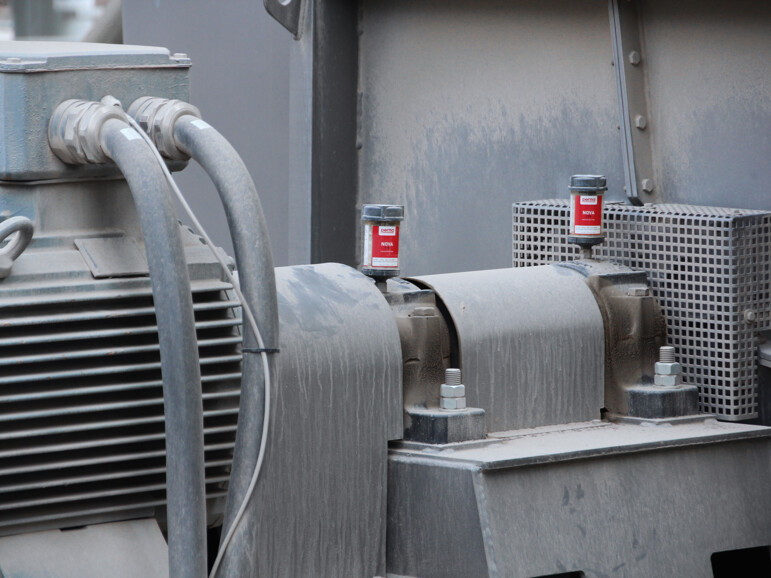
Scheduled exchanges
Scheduled exchanges of lubrication systems while machines are running reduces staff and material costs and increases economic efficiency
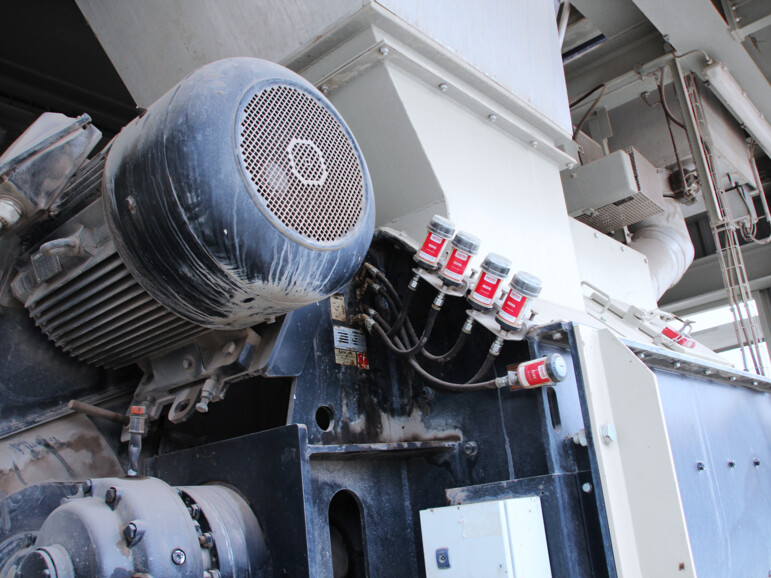
Workplace safety
Automatic lubrication away from dangerous areas increases workplace safety
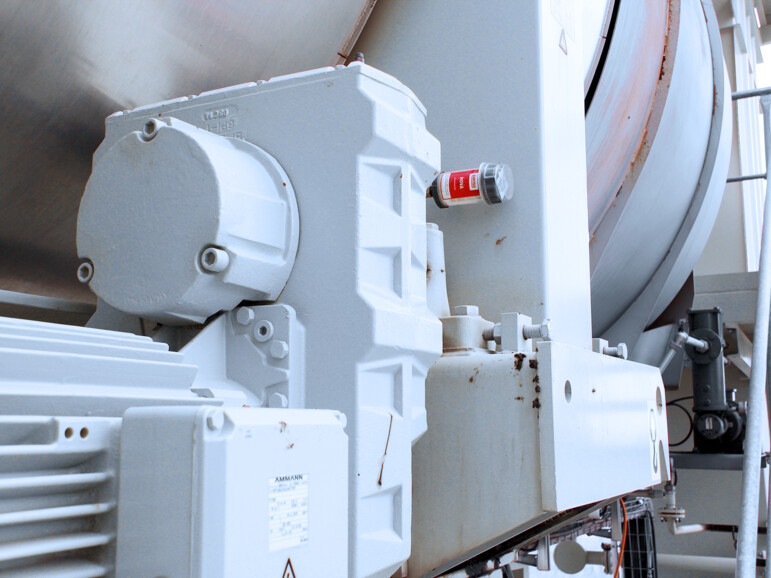
Reduces energy costs
Individual lubrication reduces energy costs by up to 10%

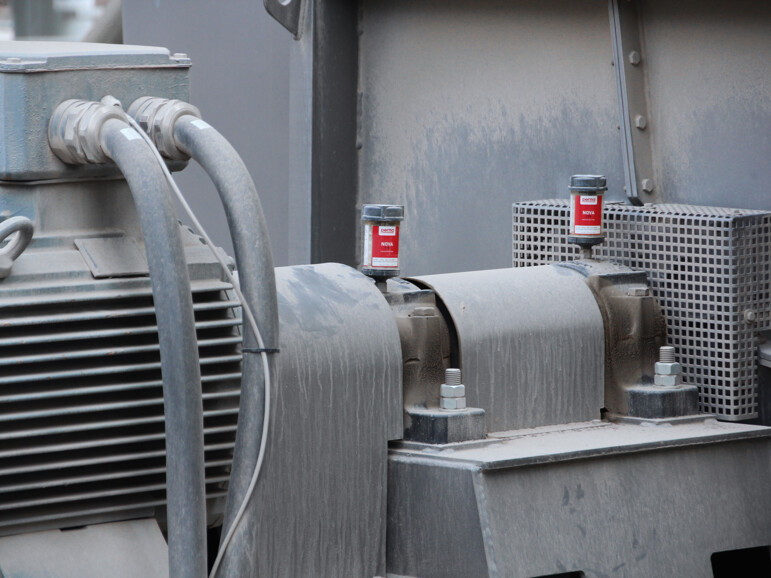
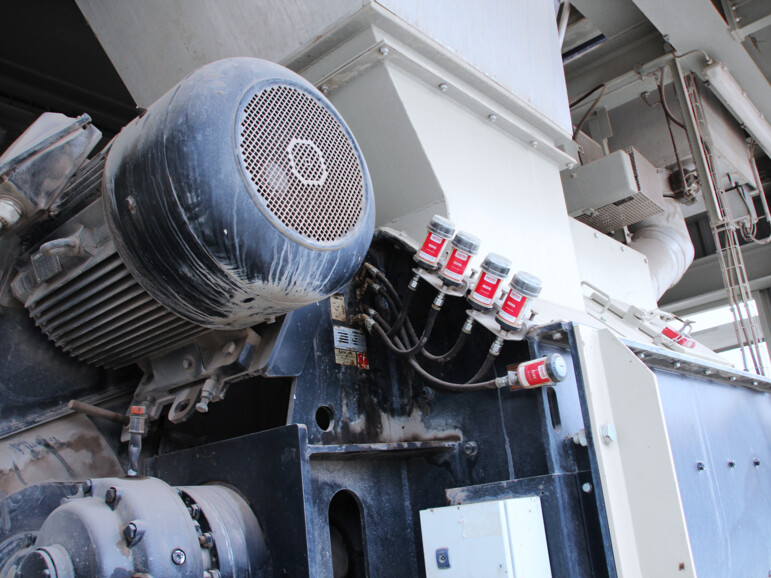
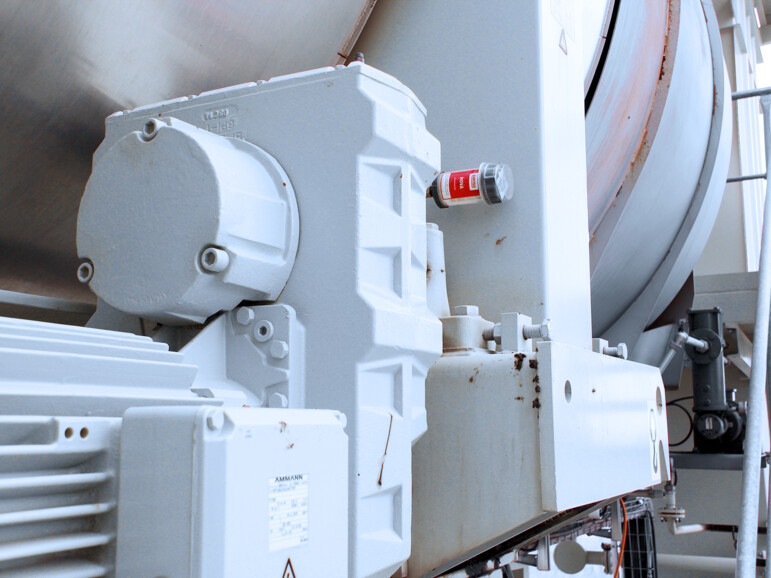
